Efficient logistics depend heavily on consistent stretch wrap machine repair services.
Efficient logistics depend heavily on consistent stretch wrap machine repair services.
Blog Article
A Comprehensive Method to Resolving Stretch Wrap Maker Repair Service Difficulties
You know that stretch wrap devices are critical for preserving efficiency in packaging operations. Issues can occur that interfere with efficiency. What are the best approaches to ensure your devices run smoothly?
Understanding Common Stretch Cover Maker Issues
When you count on stretch cover equipments for reliable product packaging, it's essential to identify typical problems that can interrupt procedures - stretch wrap machine repair. One prevalent problem is irregular stress, which can bring about insufficient wrapping and compromised tons stability. If you notice the movie isn't sticking properly, look for damaged rollers or inappropriate setups
An additional issue you may face is film damage, often triggered by incorrect film type or machine breakdowns. Consistently check the equipment for indicators of wear and tear to avoid this.
Furthermore, watch on movie buildup or jams, which can halt production. Frequently, this takes place because of misalignment or debris in the device.
Lastly, inappropriate securing can cause lots coming apart during transit. Make sure your maker is calibrated appropriately to preserve the honesty of your packages. By staying watchful and resolving these issues without delay, you can facilitate smoother operations.
The Value of Normal Preventive Maintenance
Regular preventive maintenance is necessary for keeping your stretch wrap equipment running smoothly and effectively. By routinely inspecting and servicing your devices, you can detect prospective issues prior to they escalate into pricey repair work. This proactive approach not just expands the lifespan of your machine but also assures that it operates at peak performance.
You need to set up regular inspections to tidy, lubricate, and change worn elements. Keeping your machine adjusted helps keep ideal wrapping high quality, minimizes waste, and improves performance. Additionally, documenting maintenance tasks creates a reputable background that can educate future choices.
Don't forget the relevance of training your staff on maintenance ideal techniques. When everyone recognizes how to care for the machine, you minimize the danger of driver mistake causing break downs. Simply put, dedicating to routine precautionary upkeep is a smart investment that pays off in decreased downtime and boosted efficiency in your procedures.
Repairing Strategies for Quick Services
Efficient fixing techniques can substantially minimize downtime when your stretch cover equipment runs into issues. Is the machine not wrapping effectively or is it making uncommon sounds?
Next, check the equipment's setups and controls; often, an easy change can solve the issue. Check the movie tension and placement, as inappropriate configuration can result in covering failures. Don't forget electrical links; loosened or damaged wires can disrupt functionality.
If you're still dealing with challenges, take into consideration running diagnostic examinations if your machine has that capability. Paper each step you take, as this can aid in future troubleshooting and repairs. Lastly, do not wait to speak with a professional if you can not deal with the issue quickly. Reliable troubleshooting keeps your procedures running efficiently and lessens expensive delays.
Educating Operators for Effective Maker Use
To assure your stretch wrap maker runs at peak effectiveness, correct training for operators is essential. When drivers comprehend the maker's capabilities, they can optimize its potential and decrease downtime.
Motivate them to practice under supervision, resolving any inquiries or problems they may have. Frequently arranged refresher training courses can maintain their skills sharp and aid them adjust to any kind of updates or adjustments in modern technology.
Furthermore, impart a culture of responsibility by empowering operators to report issues or recommend enhancements. This aggressive approach not only improves their self-confidence but additionally contributes to the overall efficiency of your procedures. With well-trained drivers, you'll see fewer errors and raised productivity, ensuring your stretch wrap machine continues to be a beneficial asset.
Constructing a Strong Communication Network Between Teams
Well-trained drivers can only do at their finest when there's a strong interaction channel between groups. Effective communication eliminates misconceptions and warranties everybody's on the same page relating to machine procedures and repair work demands. Motivate regular check-ins and conferences to review concerns, share understandings, and address problems.
Using innovation, like messaging apps or joint systems, can improve real-time interaction, making it much easier to report problems and share updates promptly. Appointing clear functions and duties fosters liability, allowing team participants to get to out to the best person when issues arise.
Additionally, developing an open atmosphere where everyone feels comfy sharing comments can cause innovative services. By prioritizing interaction, you're not simply boosting device efficiency; you're likewise building a natural team that interacts flawlessly. This collective spirit ultimately results in quicker repair work and lowered downtime, profiting the entire procedure.
Purchasing Top Quality Replacement Components
When it pertains to keeping your stretch wrap equipments, purchasing top quality replacement parts is crucial for making certain dependable performance and minimizing downtime. Cheap choices might seem appealing, but they usually bring about even more significant issues down the line, costing you much more out of commission and shed performance. By choosing top notch components, you're not simply taking care of an issue; you're improving the total efficiency of your devices.
Additionally, quality parts are commonly produced to more stringent criteria, which suggests they'll fit better and work more accurately. This decreases the possibility of unforeseen break downs, allowing your procedures to run smoothly. Trustworthy providers frequently offer warranties, offering you peace of mind in your investment.
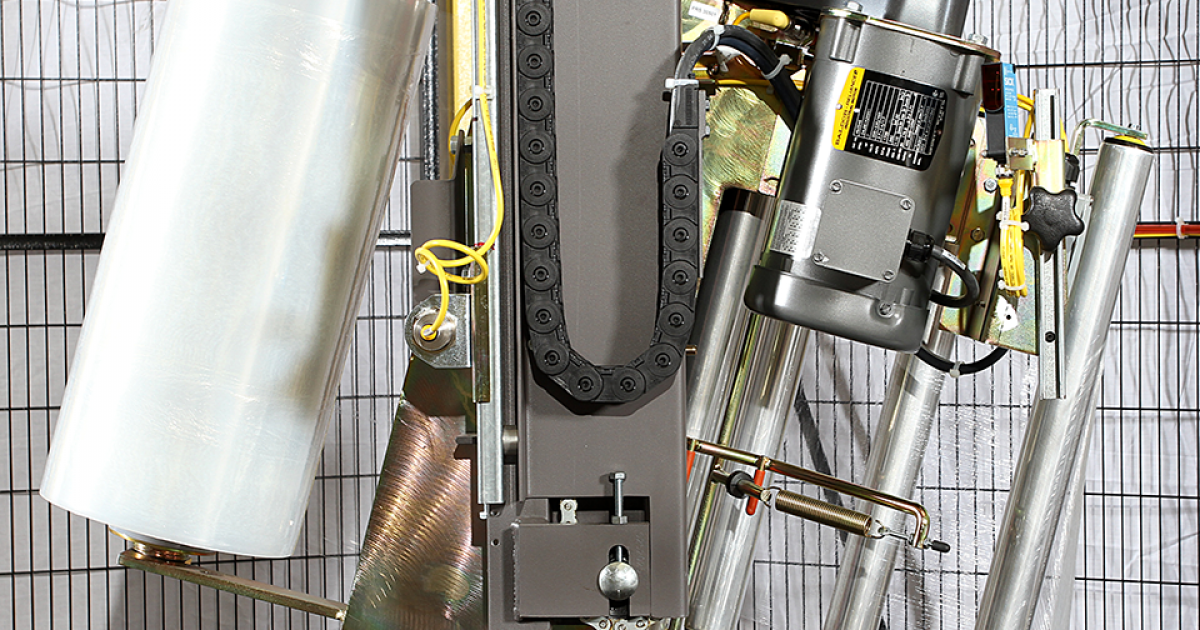
Assessing Performance Data for Continuous Renovation
To boost your stretch wrap device's efficiency, you need effective data collection techniques. By assessing efficiency metrics, you can identify locations for enhancement and boost efficiency. Identifying these possibilities not just streamlines procedures yet also decreases downtime and repair prices.
Information Collection Methods
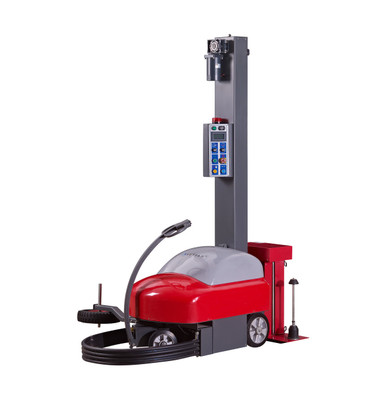
Performance Metrics Analysis
While examining performance metrics, it's crucial to focus on certain data factors that directly influence your stretch cover machine's her response performance. Begin by tracking cycle times, as they disclose exactly how promptly your maker operates under normal problems. This continuous assessment helps improve efficiency, minimize costs, and inevitably enhance your equipment's durability, leading to a more effective covering procedure in general.
Determining Improvement Opportunities
As you assess efficiency information, you can discover valuable renovation possibilities that enhance your stretch cover machine's effectiveness. Seek trends in downtime, cycle times, and cover high quality. By determining patterns, you'll see which locations require interest. For example, if frequent break downs correlate with particular operating conditions, you can change procedures to mitigate these problems. Furthermore, contrast your information versus sector standards to assess your performance. Involve your group in conversations about the findings; their understandings can expose practical options. Executing small modifications based on this analysis can cause significant gains in productivity. Routinely reviewing and updating your performance information will certainly guarantee constant renovation, keeping your operations running efficiently and properly.
Frequently Asked Questions
How Can I Tell if My Machine Requirements a Repair Service or Simply Maintenance?
To tell if your maker requires repair or just maintenance, pay attention for uncommon sounds, look for irregular efficiency, and examine for visible wear. If concerns persist after maintenance, it's most likely time for a fixing.

What Is the Average Lifespan of a Stretch Cover Equipment?
The go to these guys average life expectancy of a stretch cover maker is generally five to 10 years, depending on usage and upkeep. Regular treatment can prolong its life, so keep an eye on performance and address issues immediately.
Exist Particular Brand Names Recognized for Better Dependability?
Yes, some brands are recognized for their reliability. You'll discover that business like Signode and Lantech often receive favorable evaluations - stretch wrap machine repair. Looking into user comments can help you select a dependable stretch cover machine for your needs
What Are the Signs of Poor Operator Training?
If you discover constant mistakes, irregular covering, or security incidents, those are indicators of bad operator training. Lack of recognizing concerning maker functions or failure to follow protocols can substantially impact performance and safety.
Just How Can I Find a Certified Professional for Repairs?
To locate a qualified service technician for my response repair work, request for referrals from sector peers, check on-line evaluations, and verify qualifications. You may additionally think about getting in touch with local equipment distributors who commonly have actually trusted service technicians accessible.
Verdict
To summarize, dealing with stretch cover device repair service challenges needs a positive strategy. By prioritizing precautionary maintenance, giving detailed driver training, and investing in top quality parts, you can substantially decrease downtime and boost efficiency. Do not fail to remember the importance of solid communication between teams and constant examination of device outcome. By applying these techniques, you'll not just improve wrapping high quality but also foster a society of performance and enhancement in your procedures. Stay in advance of problems prior to they arise!
Report this page